Perfektion aus Leidenschaft
Der unbedingte Wille zur Perfektion ist die wichtigste Säule unserer Philosophie. Wir stellen uns den höchsten Anforderungen und finden einzigartige Lösungen für unsere Kunden. Unser eigener Anspruch auf Perfektion motiviert uns, permanent unser Bestes zu geben und selbstkritisch mit uns umzugehen. Dies macht uns zu einem zuverlässigen Partner. Wir sind stolz auf unsere Mitarbeiter, die dazu beitragen.
Gutes besser machen
Unser tägliches Bestreben ist es, den guten Zustand durch einen besseren zu ersetzen. Wenn diese Leistung durch unsere Kunden mit Auszeichnungen honoriert werden, ist das für uns Bestätigung und Ansporn zugleich. Unsere Leitlinien ermöglichen uns, maßgeschneiderte Lösungen anzubieten und sind uns Wegweiser für das tägliche Handeln. Der Blickwinkel unserer Geschäftsentwicklung gilt gleichermaßen unseren Mitarbeitern und unseren Kunden.
Menschen bei Otto Klumpp
Mehr noch als nur die technische Qualität unserer Produkte zählt die Kompetenz und Motivation unserer Mitarbeiter. Um die Anforderungen unserer Kunden zu erfüllen, gehen sie bis an die Grenzen des physikalisch Machbaren.
Eine hohe Motivation aller Mitarbeiter ist der Garant für Schnelligkeit und Effizienz bei der Bewältigung selbst schwierigster Aufgaben. Auf dem Gebiet des anspruchsvollen Kunststoff-Spritzgusses haben wir uns einen Namen gemacht.
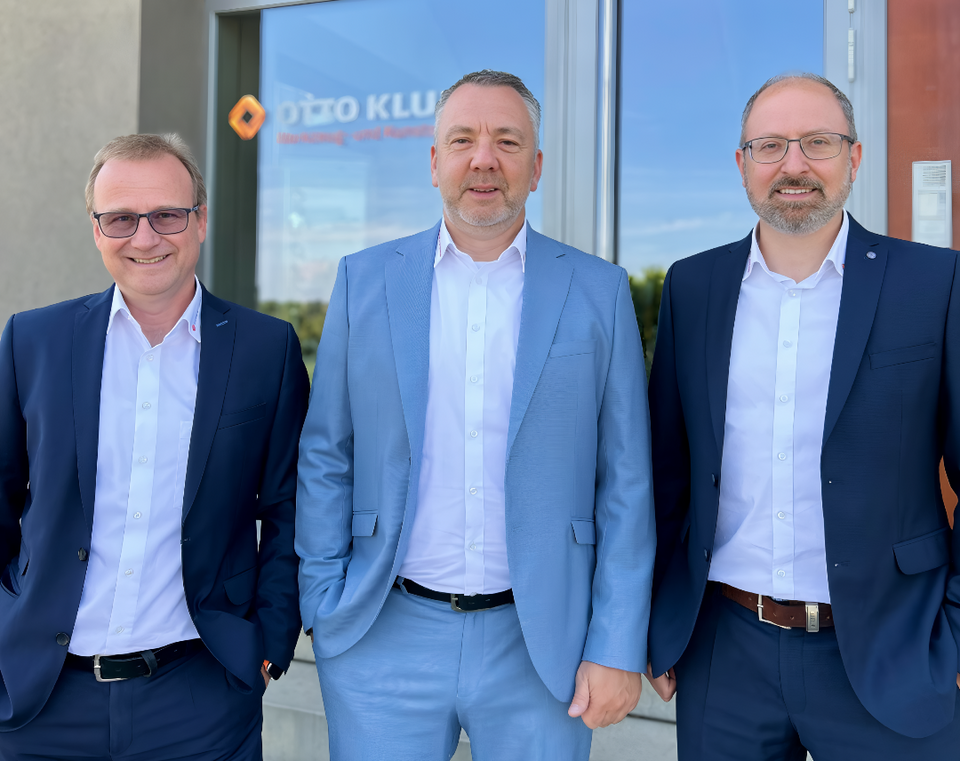
Karriere bei Otto Klumpp
Seit über 60 Jahren steht die Otto Klumpp GmbH für innovative Kompetenz und kompromisslose Qualität in der Werkzeug- und Kunststofftechnik. Mit rund 140 Mitarbeitern entwickeln, produzieren und vertreiben wir technisch anspruchsvolle Werkzeuglösungen und hochwertige thermoplastische Kunststoffspritzguss-Produkte für die Bereiche Fahrzeugtechnik, Filtrationstechnik, Medizintechnik und Industrietechnik. Um unsere Ziele – auf Basis einer wachstumsorientierten Strategie – zu realisieren, suchen wir regelmäßig motivierte Talente.
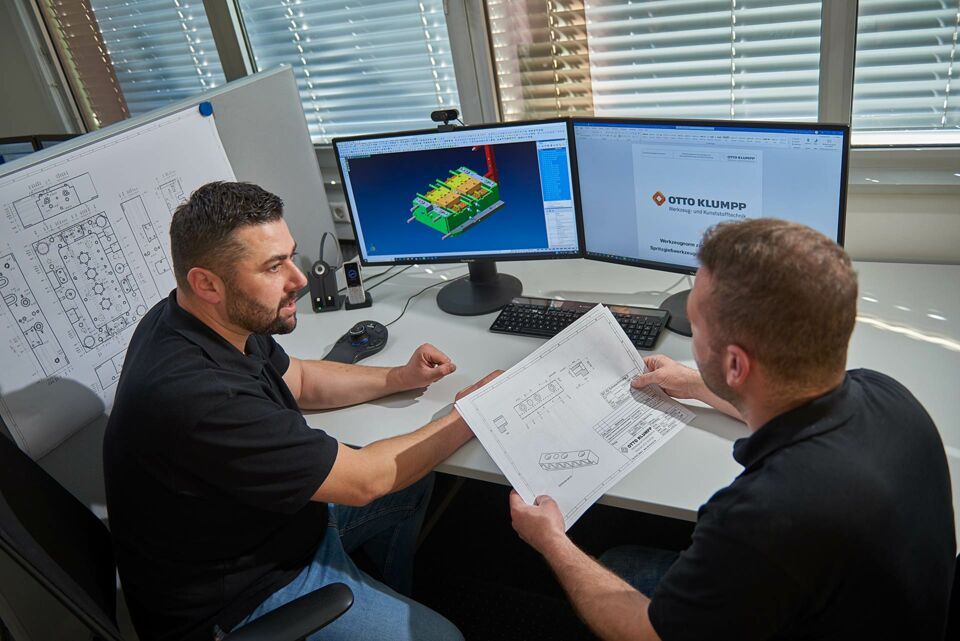
Historie
Erweiterung Maschinenpark und noch viel mehr
Inbetriebnahme der 11ten vollelektrischen Spritzgussmaschine. Isolierung, Instandhaltung von diversen Gebäuden und Gebäudedächern. Umstellung des Fuhrparks auf Hybridfahrzeuge. Einführung des Umweltmanagements und Zertifizierung nach DIN ISO 14001. Installation einer vollautomatischen 8-Fach-Produktionsanlage für einen Saugsieb. Herstellung im Insert-Moulding-Spritzguss.
Entwicklung der Umstülpetechnik:
Vollautomatischer Zuschnitt des Gewebes, Transfer, Legen und Falten der Gewebegeometrie, Umspritzen des gefalteten Gewebes zu einem Saugsieb. 100%ige Auswertung, Überprüfung und Überwachung der Filterbauteile über ein Kamerasystem, Teilablage und Verpackung der Saugsiebe.
Installation eines 3-D Messmikroskops
Optimierung Reinraum gemäß 14644
Digitalisierung:
Ausbau EDV Netzwerk, neues ERP System, neue Zeiterfassung, Leitrechneranbindung an das BDE-System, Einführung Otto Klumpp Prozesssystem
Ausrichtung des gesamten Unternehmens auf die 5S-Methode
60 Jähriges Firmenjubiläum und Erweiterung des Maschinenparks
Inbetriebnahme der 10ten vollelektrischen Spritzgussmaschine, Maschinepark besteht jetzt aus ca. 25 % vollelektrischer Spritzgussmaschinen.
Installation einer vollautomatischen 4-Fach-Produktionsanlage für einen Saugsieb.
Herstellung im Insert-Moulding-Spritzguss.
Vollautomatischer Zuschnitt des Gewebes, Tiefziehen der Filtergeometrie zu einer Halbkugel, Umspritzen der Halbkugel.
100%ige Auswertung, Überprüfung und Überwachung der Filterbauteile über ein Kamerasystem, nestbezogene Teilablage und Verpackung der Saugsiebe.
Installation einer Ultraschallreinigungsanlage für Spritzgusswerkzeug.
Erweiterung Maschinenpark
Inbetriebnahme der 9ten vollelektrische Spritzgussmaschine.
Installation einer vollautomatischen 16-Fach-Produktionsanlage für einen Last-Chance-Filter für ein Fahrzeuggetriebe.
Produktionsvolumen 20 Mio. Teile pro Jahr. Herstellung im Insert-Moulding-Spritzguss. Vollautomatischer 16-Fach-Zuschnitt des Trapezfilters, Umspritzen des Trapezfilters in einem 16-Fachwerkzeug.
100%ige Auswertung, Überprüfung und Überwachung der Filterbauteile über ein Kamerasystem, Nestbezogene Teilablage und Verpackung der Last-Chance-Filter.
Installation einer vollautomatischen 4-Fach-Produktionsanlage für einen Saugsieb
Entwicklung der Tiefzieh-Durchstanztechnik Gen 2:
Herstellung im Insert-Moulding-Spritzguss. Vollautomatischer Zuschnitt des Gewebes, Tiefen der Gewebegeometrie zu einer Halbkugel, Umspritzen der Halbkugel.
100%ige Auswertung, Überprüfung und Überwachung der Filterbauteile über ein Kamerasystem, Nestbezogene Teilablage und Verpackung der Saugsiebe. FDA Registrierung
Erweiterung Maschinenpark
Inbetriebnahme der achten vollelektrischen Spritzgussmaschine.
Bau von zwei weiteren hoch Präzision 16-Fach-Werkzeugen mit je 64 Schiebern für die Filtertechnik.
Bau und Inbetriebnahme Montagespritzgussanlage für ein Filterbauteil für die E-Mobilität. Produktionsvolumen 2 Mio. Teile/Jahr.
2+2 Fach Insert-Moulding-Spritzguss. Vollautomatischer Filterproduktion, Filterbauteil wird mit mittels Ultraschallschweißen mit einem Unterteil verschweißt. Fertige montierte Baugruppe wird in einem Transporttray einzeln abgelegt.
Inbetriebnahme der 6te vollelektrische Spritzgussmaschine
Entwicklung der Tiefzieh-Durchstanztechnik Gen. 1:
Installation einer 8-Fach vollautomatischen Produktionsanlage für einen Hutfilter mittels Insert-Moulding-Spritzguss.
Vollautomatischer Zuschnitt des Gewebes, Formung der Gewebegeometrie, Übergabe des geformten Gewebehutes in das Spritzgusswerkzeug. 100%ige Auswertung, Überprüfung und Überwachung der Filterbauteile über ein Kamerasystem. Vollautomatische 100% Dichtheitsmessung der Hutfilter 100%, Nestbezogene Teilablage und Verpackung der Hutfilter.
Start des OK4.0 Prozesses „Fit For Future“ (OK = Otto Klumpp)
Inbetriebnahme der 7te vollelektrische Spritzgussmaschine mit einer Zuhaltekraft von 230 Tonnen im Reinraum.
Erweiterung Maschinenpark
Inbetriebnahme der 5ten vollelektrischen Spritzgussmaschine und Inbetriebnahme einer Flachschleifmaschine für den Werkzeugbau.
Bau von zwei hoch Präzision 16-Fach-Werkzeugen mit 64 Schiebern für die Filtertechnik.
Produktionsvolumen 20 Mio. Teile pro Werkzeug pro Jahr.
Einstieg in den Mikrospritzguss, neue Drahterodiermaschine, Erweiterung Linearzelle um eine Fräsmaschine
Inbetriebnahme einer vollelektrischen Mikrospritzgussmaschine (Inbetriebnahme der 4ten vollelektrischen Spritzgussmaschine) und Bau von 2 8-Fach-Werkzeugen für Mikrobauteile.
AgieCharmilles CUT 3000 S, im Werkzeugbau ist jetzt eine durchgängige Genauigkeit des Maschinenparkes im Mikrometerbereich gewährleistet. Erweiterung der vollautomatischen Linearzelle um eine zweite Fräsmaschine. Die Linearzelle besteht aus einer AgieCharmilles Form 3000 HP und einer Mikron HSM 600 ULP und eine HSM 400 LP. Die drei Maschinen sind über eine 3R Workmaster verknüpft und werden von einem Zeiss Messzentrum DuraMax CNC überwacht (vollautomatische Einzelteilfertigung für den Werkzeugbau).
Inbetriebnahme der fünften Montagespritzgussanlage
Bau und Inbetriebnahme der fünften Montagespritzgussanlage, Produktionsvolumen 40 Mio. Teile/Jahr.
Installation einer vollautomatischen Produktionsanlage für einen Filterkorb im Insert-Moulding-Spritzguss.
Automatischer Zuschnitt des Gewebezylinders, Einlage des Gewebezylinders über einen 7-Achs-Roboter in das Spritzgusswerkzeug, Entnahme des fertigen Filterkorbs mit einem 2ten 7-Achs-Roboter aus dem Spritzgusswerkzeug. Kameragestützte Prüfung, Ablage und Verpackung der Filterkörbe.
Inbetriebnahme der zweiten und dritten vollelektrischen Spritzgussmaschine.
Einzug in das neue Verwaltungsgebäude
Abschluss aller in 2011 gestarteter Baumaßnahmen. Die Gesamtfläche des Unternehmens beträgt nun ca. 12.000 m².
Inbetriebnahme der neuen Lagerhalle, Zertifizierung nach ISO TS 16949
Umzug Werkzeugbau in die neue vollklimatisierte Halle, Erweiterung Maschinenpark Werkzeugbau um eine vollautomatische Linearzelle, bestehend aus einer AgieCharmilles Form 3000 HP und einer Mikron HSM 600 ULP. Die beiden Maschinen sind über eine 3R Workmaster verknüpft und werden von einer Zeiss Messzentrum DuraMax CNC überwacht (vollautomatische Einzelteilfertigung für den Werkzeugbau).
Bau und Inbetriebnahme der vierten Montagespritzgussanlage, Produktionsvolumen 32 Mio. Teile/Jahr.
Installation der ersten vollelektrischen Spritzgussmaschine.
Firmenjubiläum – 50 Jahre Otto Klumpp, Werksoptimierung
Otto Klumpp wird 50.
Außerdem starten wir am 01.08.2011 mit unserer Werkserweiterung. Das Bauprojekt ist in 3 Bauphasen unterteilt:
1. Erstellung Lagerhalle mit Freilager, Betriebshof und MA-Parkplätze.
2. Erweiterung vollklimatisierte Produktionshalle für den Werkzeugbau.
3. Erweiterung Verwaltungsgebäude und Außenanlagen.
Das Bauvorhaben wird auf Basis der im Vorfeld durchgeführten Werksstrukturoptimierung ausgeführt. Wir verfolgen damit das Ziel konsequent optimale Produktions- und Logistikabläufe verwirklichen zu können.
Lieferantenaward WOCO → Otto Klumpp wird zum besten Lieferanten gekürt „Lieferant des Jahres 2010“
Reinraum-Halle, 6-Achs-Fertigung, Face-Lift Otto Klumpp
Umbau Produktionshalle zur abgekapselten Reinraumfertigung der Reinheitsklasse 8 (100.000) mit einer weiteren Reinraumfertigung der Reinheitsklasse 7 (10.000) für die Herstellung von Produkten mit höchsten Sauberkeitsanforderungen, z. B. Medizintechnik, Filtertechnik. Inbetriebnahme einer Fertigungszelle mit 6-Achs-Roboter und Kamerasystem. Otto Klumpp bekommt ein neues Gesicht.
Einführung Werkerselbstkontrolle, Zert. DIN ISO 13485, Erweiterung Reinraum, Modernisierung Maschinenpark, Montagespritzgussanlage
Einführung Werkerselbstkontrolle im Bereich Kunststofftechnik. Zertifiziert nach Qualitätsmanagementsystem für Medizinprodukte DIN ISO 13485:2003.
Erweiterung der Reinraumproduktion auf 500 m² mit einer Reinheitsklasse 7 (10.000) und einer Produktionskapazität von 9 Spritzgießmaschinen mit einer Zuhaltung von 25 t bis 280 t.
Installation einer 3D-Multi-Sensorik-Messmaschine.
Installation einer 5-Achs-Fräsmaschine. Bau und Inbetriebnahme der dritten Montagespritzgussanlage, Produktionsvolumen 24 Mio. Teile/Jahr.
Erweiterung Maschinenpark Werkzeugbau, Software-Umstellung
Installation einer weiteren Drahterodiermaschine im Bereich Werkzeugbau. Außerdem erfolgt die Umstellung der CAD-Software. Sämtliche Arbeitsplätze in Vertrieb, Projektierung und innerhalb der Fertigungsbereiche Werkzeug und Kunststofftechnik sind mindestens mit einem 3D-Viewer ausgestattet.
Modernisierung Maschinenpark Werkzeugbau
Installation eines Vertikalbearbeitungszentrums im Bereich Werkzeugtechnik.
Installation einer weiteren Montagespritzgussanlage
Bau und Inbetriebnahme der zweiten Montagespritzgussanlage mit integrierter Prozess- und Spezifikationsüberwachung. Produktionsvolumen 16 Mio. Teile/Jahr.
Zertifizierung nach VDA 6.1, Installation CAQ-Software, Installation Montagespritzguss (Mehrkomponentenspritzguss)
Zur Zertifizierung DIN ISO 9001 erfolgt die Zertifizierung nach VDA 6.1. Implementierung einer rechnerunterstützten Qualitätskontrolle -> CAQ-Software.
Go-live mit dem Montagespritzgussverfahren, mit integrierter Prozess und Spezifikationsüberwachung, Produktionsvolumen 8 Mio. Teile/Jahr.
Modernisierung Maschinenpark, Software-Umstellung
Installation einer zentralen Materialversorgungsanlage, die den Großmaschinenbereich von einem zentralen Punkt aus bedient. Umstellung auf ein neues ERP-System, welches den Ablauf im kunststoffverarbeitenden Unternehmen besser unterstützt.
Erweiterung der Firmengebäude
Erweiterung der Firmengebäude um weitere 1.400 m². Die Gesamtfläche des Unternehmens beträgt nun ca. 9.000 m². Außerdem wird für die Fertigung Kunststofftechnik eine Spritzgussmaschine mit einer Zuhaltung von 1.600 t aufgebaut. Auf dieser Maschine können Kunststoffteile mit einem Eigengewicht bis zu 9,00 kg gefertigt werden. Das mögliche Produktspektrum reicht nun von Teilen mit einem Gewicht von 0,004 g bis 9.000 g.
Erweiterung EDV
Installation eines BDE-Systems für den Fertigungsbereich.
Einstieg in die Medizintechnik
Inbetriebnahme der Reinraumfertigung Klasse 7 (10.000) für die Herstellung von medizintechnischen Produkten.
Zertifiziert nach DIN ISO 9001
Erfolgreiche Zertifizierung nach DIN ISO 9001.
Modernisierung der Firmengebäude
Das gesamte Unternehmen wird mit einer Sprinkleranlage ausgestattet.
Einstieg in CAD/CAM-Technologie
Installation einer CAD-Anlage. Anschaffung einer Spritzgussmaschine mit 1.050 Tonnen Schließkraft.
Erweiterung der Firmengebäude
Im neu erstellten Gebäude mit einer Fläche von 1.800 m² werden Versand, Fertigwarenlager und Montageplätze untergebracht.
Modernisierung Verwaltung
Die bestehenden Büroräume werden modernisiert und erweitert.
Erweiterung der Firmengebäude
Erweiterung der Kunststoffverarbeitung um weitere 800 m².
Erweiterung der Firmengebäude
Umzug der Fertigung Werkzeugbau in ein neu erstelltes Fertigungsgebäude mit 840 m².
Erweiterung der Firmengebäude und des Maschinenparks
Anschaffung einer Spritzgussmaschine mit 150 t Zuhaltekraft. Diese wird in der neu erstellten Produktionshalle aufgestellt.
Erweiterung des Maschinenparks
Zur Veredelung von Kunststoffartikeln wird ein Lackierstand mit Trockenband installiert.
Einstieg in die Kunststofftechnik
Anschaffung der ersten Kunststoffspritzgussmaschine. Der Einstieg in die Kunststofftechnik beginnt damit, dass Werkzeuge im Haus abgemustert werden sowie erste Schritte in der Serienproduktion von Kunststoff-Spritzguss-Artikeln gemacht werden.
Erweiterung der Firmengebäude
Vergrößerung der Firmengebäude um 560 m².
Erstes Firmengebäude, Einstieg in die Werkzeugtechnik
Das Firmengebäude wird in der Burgstraße 18 mit einer Fläche von 220 m² errichtet, in dem der Werkzeugbau und die Büroräume untergebracht werden.
Werkzeugtechnik
In den folgenden Jahren werden verstärkt Schnitt-, Stanz- und Folgeverbundwerkzeuge gefertigt. Zudem hält die zum damaligen Zeitpunkt noch sehr junge Technologie Werkzeugtechnik im Hause Klumpp Einzug. Von nun an werden Spritzgusswerkzeuge konstruiert und gefertigt.
Firmengründung durch Otto Klumpp
Die Firma Otto Klumpp wird gegründet, in der mechanische Arbeiten wie Bohren, Drehen und Fräsen durchgeführt werden. Im selben Jahr wird mit der Anschaffung einer Spitzendrehbank der Grundstein für den heutigen Betrieb gelegt. Von nun an können zu den mechanischen Arbeiten auch Präzisionsteile gefertigt werden.
2022Erweiterung Maschinenpark und noch viel mehr
Inbetriebnahme der 11ten vollelektrischen Spritzgussmaschine. Isolierung, Instandhaltung von diversen Gebäuden und Gebäudedächern. Umstellung des Fuhrparks auf Hybridfahrzeuge. Einführung des Umweltmanagements und Zertifizierung nach DIN ISO 14001. Installation einer vollautomatischen 8-Fach-Produktionsanlage für einen Saugsieb. Herstellung im Insert-Moulding-Spritzguss.
Entwicklung der Umstülpetechnik:
Vollautomatischer Zuschnitt des Gewebes, Transfer, Legen und Falten der Gewebegeometrie, Umspritzen des gefalteten Gewebes zu einem Saugsieb. 100%ige Auswertung, Überprüfung und Überwachung der Filterbauteile über ein Kamerasystem, Teilablage und Verpackung der Saugsiebe.
Installation eines 3-D Messmikroskops
Optimierung Reinraum gemäß 14644
Digitalisierung:
Ausbau EDV Netzwerk, neues ERP System, neue Zeiterfassung, Leitrechneranbindung an das BDE-System, Einführung Otto Klumpp Prozesssystem
Ausrichtung des gesamten Unternehmens auf die 5S-Methode
202160 Jähriges Firmenjubiläum und Erweiterung des Maschinenparks
Inbetriebnahme der 10ten vollelektrischen Spritzgussmaschine, Maschinepark besteht jetzt aus ca. 25 % vollelektrischer Spritzgussmaschinen.
Installation einer vollautomatischen 4-Fach-Produktionsanlage für einen Saugsieb.
Herstellung im Insert-Moulding-Spritzguss.
Vollautomatischer Zuschnitt des Gewebes, Tiefziehen der Filtergeometrie zu einer Halbkugel, Umspritzen der Halbkugel.
100%ige Auswertung, Überprüfung und Überwachung der Filterbauteile über ein Kamerasystem, nestbezogene Teilablage und Verpackung der Saugsiebe.
Installation einer Ultraschallreinigungsanlage für Spritzgusswerkzeug.
2020Erweiterung Maschinenpark
Inbetriebnahme der 9ten vollelektrische Spritzgussmaschine.
Installation einer vollautomatischen 16-Fach-Produktionsanlage für einen Last-Chance-Filter für ein Fahrzeuggetriebe.
Produktionsvolumen 20 Mio. Teile pro Jahr. Herstellung im Insert-Moulding-Spritzguss. Vollautomatischer 16-Fach-Zuschnitt des Trapezfilters, Umspritzen des Trapezfilters in einem 16-Fachwerkzeug.
100%ige Auswertung, Überprüfung und Überwachung der Filterbauteile über ein Kamerasystem, Nestbezogene Teilablage und Verpackung der Last-Chance-Filter.
2019Installation einer vollautomatischen 4-Fach-Produktionsanlage für einen Saugsieb
Entwicklung der Tiefzieh-Durchstanztechnik Gen 2:
Herstellung im Insert-Moulding-Spritzguss. Vollautomatischer Zuschnitt des Gewebes, Tiefen der Gewebegeometrie zu einer Halbkugel, Umspritzen der Halbkugel.
100%ige Auswertung, Überprüfung und Überwachung der Filterbauteile über ein Kamerasystem, Nestbezogene Teilablage und Verpackung der Saugsiebe. FDA Registrierung
2018Erweiterung Maschinenpark
Inbetriebnahme der achten vollelektrischen Spritzgussmaschine.
Bau von zwei weiteren hoch Präzision 16-Fach-Werkzeugen mit je 64 Schiebern für die Filtertechnik.
Bau und Inbetriebnahme Montagespritzgussanlage für ein Filterbauteil für die E-Mobilität. Produktionsvolumen 2 Mio. Teile/Jahr.
2+2 Fach Insert-Moulding-Spritzguss. Vollautomatischer Filterproduktion, Filterbauteil wird mit mittels Ultraschallschweißen mit einem Unterteil verschweißt. Fertige montierte Baugruppe wird in einem Transporttray einzeln abgelegt.
2017Inbetriebnahme der 6te vollelektrische Spritzgussmaschine
Entwicklung der Tiefzieh-Durchstanztechnik Gen. 1:
Installation einer 8-Fach vollautomatischen Produktionsanlage für einen Hutfilter mittels Insert-Moulding-Spritzguss.
Vollautomatischer Zuschnitt des Gewebes, Formung der Gewebegeometrie, Übergabe des geformten Gewebehutes in das Spritzgusswerkzeug. 100%ige Auswertung, Überprüfung und Überwachung der Filterbauteile über ein Kamerasystem. Vollautomatische 100% Dichtheitsmessung der Hutfilter 100%, Nestbezogene Teilablage und Verpackung der Hutfilter.
Start des OK4.0 Prozesses „Fit For Future“ (OK = Otto Klumpp)
Inbetriebnahme der 7te vollelektrische Spritzgussmaschine mit einer Zuhaltekraft von 230 Tonnen im Reinraum.
2016Erweiterung Maschinenpark
Inbetriebnahme der 5ten vollelektrischen Spritzgussmaschine und Inbetriebnahme einer Flachschleifmaschine für den Werkzeugbau.
Bau von zwei hoch Präzision 16-Fach-Werkzeugen mit 64 Schiebern für die Filtertechnik.
Produktionsvolumen 20 Mio. Teile pro Werkzeug pro Jahr.
2015Einstieg in den Mikrospritzguss, neue Drahterodiermaschine, Erweiterung Linearzelle um eine Fräsmaschine
Inbetriebnahme einer vollelektrischen Mikrospritzgussmaschine (Inbetriebnahme der 4ten vollelektrischen Spritzgussmaschine) und Bau von 2 8-Fach-Werkzeugen für Mikrobauteile.
AgieCharmilles CUT 3000 S, im Werkzeugbau ist jetzt eine durchgängige Genauigkeit des Maschinenparkes im Mikrometerbereich gewährleistet. Erweiterung der vollautomatischen Linearzelle um eine zweite Fräsmaschine. Die Linearzelle besteht aus einer AgieCharmilles Form 3000 HP und einer Mikron HSM 600 ULP und eine HSM 400 LP. Die drei Maschinen sind über eine 3R Workmaster verknüpft und werden von einem Zeiss Messzentrum DuraMax CNC überwacht (vollautomatische Einzelteilfertigung für den Werkzeugbau).
2014Inbetriebnahme der fünften Montagespritzgussanlage
Bau und Inbetriebnahme der fünften Montagespritzgussanlage, Produktionsvolumen 40 Mio. Teile/Jahr.
Installation einer vollautomatischen Produktionsanlage für einen Filterkorb im Insert-Moulding-Spritzguss.
Automatischer Zuschnitt des Gewebezylinders, Einlage des Gewebezylinders über einen 7-Achs-Roboter in das Spritzgusswerkzeug, Entnahme des fertigen Filterkorbs mit einem 2ten 7-Achs-Roboter aus dem Spritzgusswerkzeug. Kameragestützte Prüfung, Ablage und Verpackung der Filterkörbe.
Inbetriebnahme der zweiten und dritten vollelektrischen Spritzgussmaschine.
2013Einzug in das neue Verwaltungsgebäude
Abschluss aller in 2011 gestarteter Baumaßnahmen. Die Gesamtfläche des Unternehmens beträgt nun ca. 12.000 m².
2012Inbetriebnahme der neuen Lagerhalle, Zertifizierung nach ISO TS 16949
Umzug Werkzeugbau in die neue vollklimatisierte Halle, Erweiterung Maschinenpark Werkzeugbau um eine vollautomatische Linearzelle, bestehend aus einer AgieCharmilles Form 3000 HP und einer Mikron HSM 600 ULP. Die beiden Maschinen sind über eine 3R Workmaster verknüpft und werden von einer Zeiss Messzentrum DuraMax CNC überwacht (vollautomatische Einzelteilfertigung für den Werkzeugbau).
Bau und Inbetriebnahme der vierten Montagespritzgussanlage, Produktionsvolumen 32 Mio. Teile/Jahr.
Installation der ersten vollelektrischen Spritzgussmaschine.
2011Firmenjubiläum – 50 Jahre Otto Klumpp, Werksoptimierung
Otto Klumpp wird 50.
Außerdem starten wir am 01.08.2011 mit unserer Werkserweiterung. Das Bauprojekt ist in 3 Bauphasen unterteilt:
1. Erstellung Lagerhalle mit Freilager, Betriebshof und MA-Parkplätze.
2. Erweiterung vollklimatisierte Produktionshalle für den Werkzeugbau.
3. Erweiterung Verwaltungsgebäude und Außenanlagen.
Das Bauvorhaben wird auf Basis der im Vorfeld durchgeführten Werksstrukturoptimierung ausgeführt. Wir verfolgen damit das Ziel konsequent optimale Produktions- und Logistikabläufe verwirklichen zu können.
Lieferantenaward WOCO → Otto Klumpp wird zum besten Lieferanten gekürt „Lieferant des Jahres 2010“
2010Reinraum-Halle, 6-Achs-Fertigung, Face-Lift Otto Klumpp
Umbau Produktionshalle zur abgekapselten Reinraumfertigung der Reinheitsklasse 8 (100.000) mit einer weiteren Reinraumfertigung der Reinheitsklasse 7 (10.000) für die Herstellung von Produkten mit höchsten Sauberkeitsanforderungen, z. B. Medizintechnik, Filtertechnik. Inbetriebnahme einer Fertigungszelle mit 6-Achs-Roboter und Kamerasystem. Otto Klumpp bekommt ein neues Gesicht.
2008Einführung Werkerselbstkontrolle, Zert. DIN ISO 13485, Erweiterung Reinraum, Modernisierung Maschinenpark, Montagespritzgussanlage
Einführung Werkerselbstkontrolle im Bereich Kunststofftechnik. Zertifiziert nach Qualitätsmanagementsystem für Medizinprodukte DIN ISO 13485:2003.
Erweiterung der Reinraumproduktion auf 500 m² mit einer Reinheitsklasse 7 (10.000) und einer Produktionskapazität von 9 Spritzgießmaschinen mit einer Zuhaltung von 25 t bis 280 t.
Installation einer 3D-Multi-Sensorik-Messmaschine.
Installation einer 5-Achs-Fräsmaschine. Bau und Inbetriebnahme der dritten Montagespritzgussanlage, Produktionsvolumen 24 Mio. Teile/Jahr.
2007Erweiterung Maschinenpark Werkzeugbau, Software-Umstellung
Installation einer weiteren Drahterodiermaschine im Bereich Werkzeugbau. Außerdem erfolgt die Umstellung der CAD-Software. Sämtliche Arbeitsplätze in Vertrieb, Projektierung und innerhalb der Fertigungsbereiche Werkzeug und Kunststofftechnik sind mindestens mit einem 3D-Viewer ausgestattet.
2006Modernisierung Maschinenpark Werkzeugbau
Installation eines Vertikalbearbeitungszentrums im Bereich Werkzeugtechnik.
2005Installation einer weiteren Montagespritzgussanlage
Bau und Inbetriebnahme der zweiten Montagespritzgussanlage mit integrierter Prozess- und Spezifikationsüberwachung. Produktionsvolumen 16 Mio. Teile/Jahr.
2004Zertifizierung nach VDA 6.1, Installation CAQ-Software, Installation Montagespritzguss (Mehrkomponentenspritzguss)
Zur Zertifizierung DIN ISO 9001 erfolgt die Zertifizierung nach VDA 6.1. Implementierung einer rechnerunterstützten Qualitätskontrolle -> CAQ-Software.
Go-live mit dem Montagespritzgussverfahren, mit integrierter Prozess und Spezifikationsüberwachung, Produktionsvolumen 8 Mio. Teile/Jahr.
2003Modernisierung Maschinenpark, Software-Umstellung
Installation einer zentralen Materialversorgungsanlage, die den Großmaschinenbereich von einem zentralen Punkt aus bedient. Umstellung auf ein neues ERP-System, welches den Ablauf im kunststoffverarbeitenden Unternehmen besser unterstützt.
2001Erweiterung der Firmengebäude
Erweiterung der Firmengebäude um weitere 1.400 m². Die Gesamtfläche des Unternehmens beträgt nun ca. 9.000 m². Außerdem wird für die Fertigung Kunststofftechnik eine Spritzgussmaschine mit einer Zuhaltung von 1.600 t aufgebaut. Auf dieser Maschine können Kunststoffteile mit einem Eigengewicht bis zu 9,00 kg gefertigt werden. Das mögliche Produktspektrum reicht nun von Teilen mit einem Gewicht von 0,004 g bis 9.000 g.
2000Erweiterung EDV
Installation eines BDE-Systems für den Fertigungsbereich.
1998Einstieg in die Medizintechnik
Inbetriebnahme der Reinraumfertigung Klasse 7 (10.000) für die Herstellung von medizintechnischen Produkten.
1997Zertifiziert nach DIN ISO 9001
Erfolgreiche Zertifizierung nach DIN ISO 9001.
1991Modernisierung der Firmengebäude
Das gesamte Unternehmen wird mit einer Sprinkleranlage ausgestattet.
1988Einstieg in CAD/CAM-Technologie
Installation einer CAD-Anlage. Anschaffung einer Spritzgussmaschine mit 1.050 Tonnen Schließkraft.
1987Erweiterung der Firmengebäude
Im neu erstellten Gebäude mit einer Fläche von 1.800 m² werden Versand, Fertigwarenlager und Montageplätze untergebracht.
1986Modernisierung Verwaltung
Die bestehenden Büroräume werden modernisiert und erweitert.
1985Erweiterung der Firmengebäude
Erweiterung der Kunststoffverarbeitung um weitere 800 m².
1983Erweiterung der Firmengebäude
Umzug der Fertigung Werkzeugbau in ein neu erstelltes Fertigungsgebäude mit 840 m².
1972Erweiterung der Firmengebäude und des Maschinenparks
Anschaffung einer Spritzgussmaschine mit 150 t Zuhaltekraft. Diese wird in der neu erstellten Produktionshalle aufgestellt.
1971Erweiterung des Maschinenparks
Zur Veredelung von Kunststoffartikeln wird ein Lackierstand mit Trockenband installiert.
1970Einstieg in die Kunststofftechnik
Anschaffung der ersten Kunststoffspritzgussmaschine. Der Einstieg in die Kunststofftechnik beginnt damit, dass Werkzeuge im Haus abgemustert werden sowie erste Schritte in der Serienproduktion von Kunststoff-Spritzguss-Artikeln gemacht werden.
1969Erweiterung der Firmengebäude
Vergrößerung der Firmengebäude um 560 m².
1963Erstes Firmengebäude, Einstieg in die Werkzeugtechnik
Das Firmengebäude wird in der Burgstraße 18 mit einer Fläche von 220 m² errichtet, in dem der Werkzeugbau und die Büroräume untergebracht werden.
Werkzeugtechnik
In den folgenden Jahren werden verstärkt Schnitt-, Stanz- und Folgeverbundwerkzeuge gefertigt. Zudem hält die zum damaligen Zeitpunkt noch sehr junge Technologie Werkzeugtechnik im Hause Klumpp Einzug. Von nun an werden Spritzgusswerkzeuge konstruiert und gefertigt.
1961Firmengründung durch Otto Klumpp
Die Firma Otto Klumpp wird gegründet, in der mechanische Arbeiten wie Bohren, Drehen und Fräsen durchgeführt werden. Im selben Jahr wird mit der Anschaffung einer Spitzendrehbank der Grundstein für den heutigen Betrieb gelegt. Von nun an können zu den mechanischen Arbeiten auch Präzisionsteile gefertigt werden.
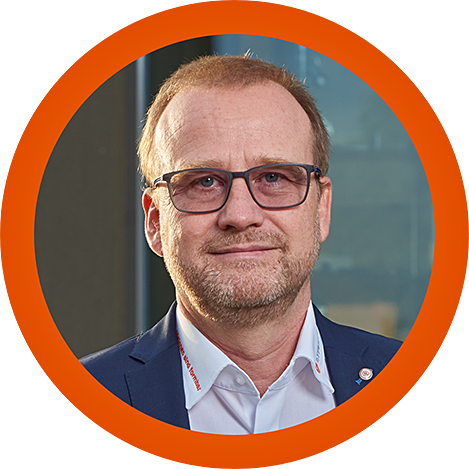
»Der Mix macht's. Die Synergieeffekte zwischen kleinen und großen Formen machen unsere Werkzeuge intelligenter.«
MARTIN KLUMPP
Geschäftsführer der Otto Klumpp GmbH